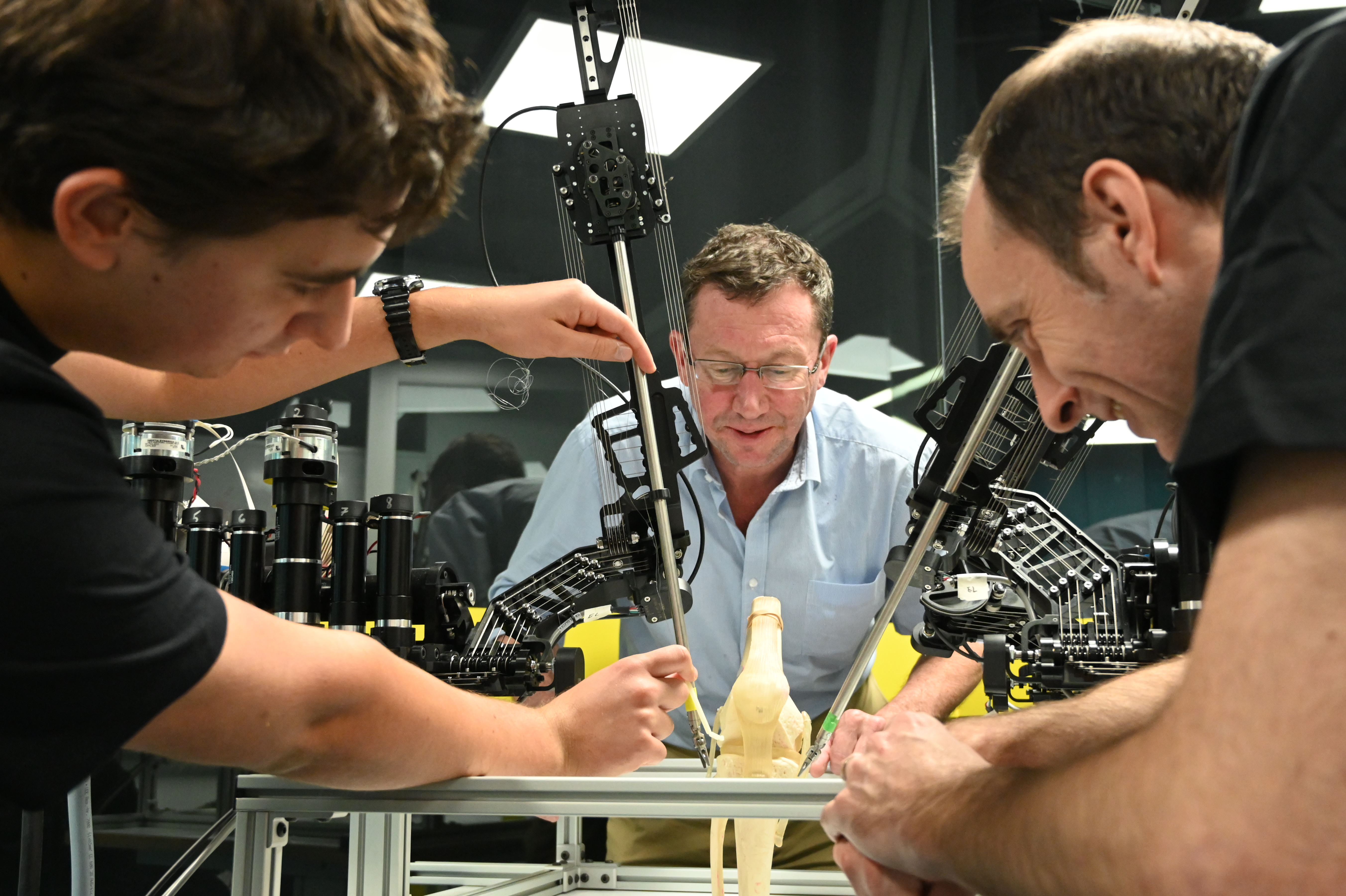
Miniature surgical robots that are unique to the individual patient’s anatomy are being created by researchers from the Australian Centre for Robotic Vision. At the head of this project is Andrew Razjigaev, who first created a snake-like robot prototype to aid in knee arthroscopy last November. Razjigaev now plans to create multiple SnakeBots that attach to a RAVEN II surgical robotic platform, working together to enhance operations. These devices are 3D printed at a low cost to fit the specific dimensions inside a patient’s knee.
The computational design algorithm used in this project generates on-of-a-kind SnakeBots that are unique to each individual patient’s body. The chosen design is most suited to fit in and flexibly move around within the joint capsule. The SnakeBot allows the surgeon to see inside the knee as well as manipulate tools for the operation. The inexpensive, 3D printed device is disposable as well.
This robotic surgical system has the power to revolutionize scope-driven surgeries, according to Jonathan Roberts, Centre Chief Investigator of the Queensland University of Technology-based Medical and Healthcare Robotics Group, and Associate Investigator Ross Crawford. Crawford is also a practicing orthopedic surgeon; therefore, he is very familiar with arthroscopic operations of the knee.
Crawford emphasized that the robotic system is not designed to replace the surgeon, but rather to assist them in improving surgical outcomes.
“At the moment surgeons use what are best described as rigid ‘one-size-fits-all’ tools for knee arthroscopy procedures, even though patients and their anatomy can vary significantly,” he explained. The surgical system is still being explored according to Crawford, and he feels it has the power to outperform current arthroscopic surgery tools.
READ MORE: Top 5 Robotic Surgery Systems
“The research project aims to design snake-like robots as miniaturized and highly dexterous surgical tools, fitted with computer vision capabilities and the ability to navigate around obstacles in confined spaces such as the anatomy of the human body,” Crawford added. “Dexterity is incredibly important as the robots are not only required to reach surgical sites but perform complicated surgical procedures via telemanipulation.”
Professor Roberts noted that this project was a first for robotics in knee arthroscopy and that the work was a culmination of several experts from the Australian Centre for Robotic Vision.
“One of the most exciting things about this project is that it is bringing many ideas from the robotics community together to form a practical solution to a real-world problem,” he said. “The project has been proceeding at a rapid pace, mainly due to the hard work and brilliance of Andrew, supported by a team of advisors with backgrounds in mechanical engineering, mechatronics, aerospace, medicine, biology, physics and chemistry.”
SnakeBot Operation: Start to Finish
The procedure begins with a scan of the patient’s knee to image its internal structure. The physician then oversees computer classification for regions that the SnakeBots should reach within the knee and others that it should avoid. This process generates a 3D environment for the SnakeBots to “compete” in, simulating the evolution process. Only the SnakeBot that is best suited for the reconstructed environment is selected.
This allows for multiple SnakeBots to be tested and evaluated based on their performance within the knee. Black lines in the image show the trajectories that a SnakeBot takes in moving to certain sites. The evolution-based algorithm then continually makes new generations of SnakeBots that are evaluated. In this “survival of the fittest” process, only the best suited SnakeBot to the patient’s knee is selected. This is the robotic device that can safely reach target zones within the knee without causing harm.
These SnakeBots that win the evolution battle are created into 3D printing models that can be created at low cost. Being that the SnakeBot is unique to the individual patient, the device is disposable after each operation.
Once employed for surgery, the device is attached to a larger, robotic platform that properly maneuvers them for entry into incision sites. The plan is for two SnakeBots to be equipped with surgical instruments, allowing the surgeon to perform dual-arm procedures.
The third SnakeBot involved is armed with the camera that allows surgeons to view inside the joint capsule. This camera will also serve as the eyes for the other SnakeBots, mapping out the joint so that they can be properly maneuvered within the knee. This camera will track both arms simultaneously.
“Surgeons want to do the best they can and face a lot of challenges,” Andrew concluded. “Our objective is to provide surgeons with new tools to be able to perform existing surgery, like knee arthroscopy, more efficiently and safely and to perhaps perform surgery that is simply too difficult to attempt with today’s tools. It’s also incredibly cool to use evolution in my work! There’s no question we’re witnessing the age-old process – the only difference being it’s happening inside a computer instead of nature.”
Custom 3D Printed Robotic Surgical Instruments for Every Patient https://t.co/OQkOi0aWNE #OrthopedicSurgery #Surgery pic.twitter.com/vC6GT3kkQU
— Medgadget (@Medgadget) July 12, 2019