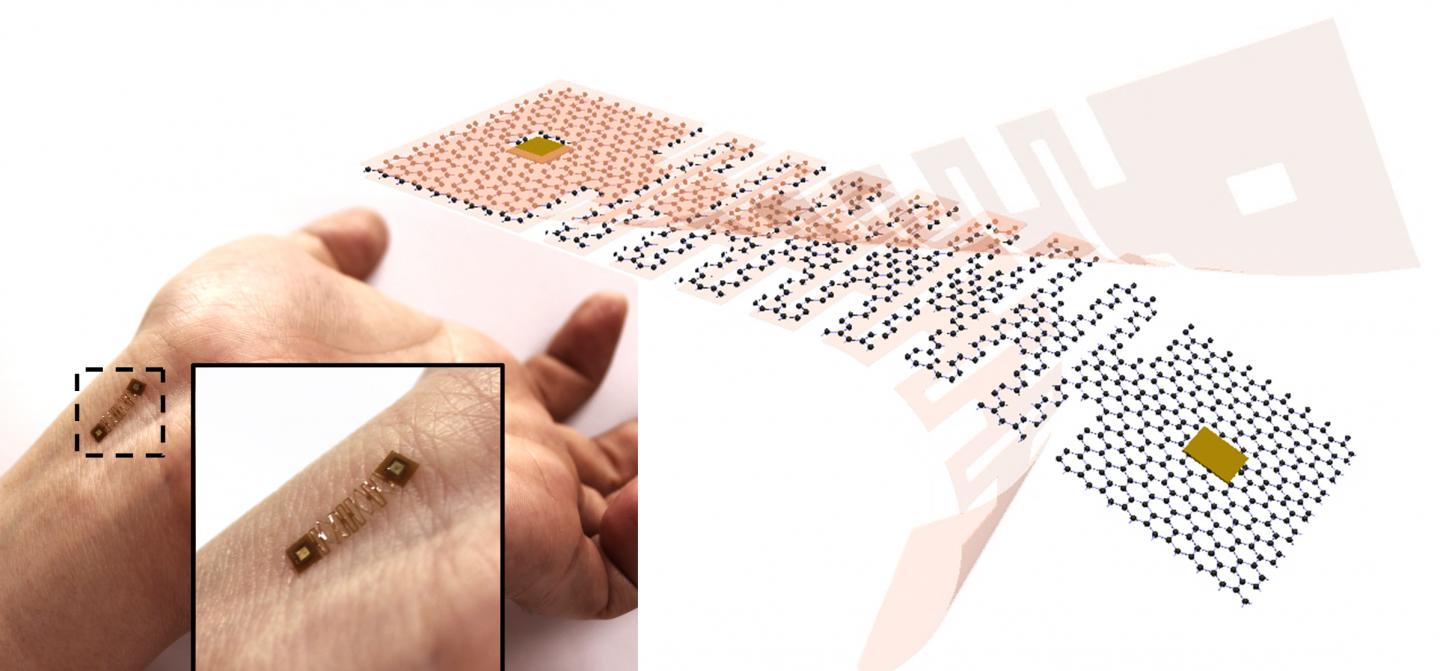
A research team from the University of Illinois at Urbana-Champaign (UIUC) has recently used an origami-like technique to better shape wearable sensor materials to handle strains from the body’s movement. The paper folding technique used in this work, kirigami, involves cutting in addition to the folding of material to create unique designs. Led by UIUC’s SungWoo Nam, PhD, and Keong Yong, graduate research assistant, the team was able to apply kirigami techniques to graphene, an ultra-thin, flexible, and strong material to make sensors that are fit for wearable devices. Their work was published recently in the journal Materials Today.
“To achieve the best sensing results, you don’t want your movement to generate additional signal outputs,” explained Nam, associate professor of Mechanical Science and Engineering. “We use kirigami cuts to provide stretchability beyond a material’s normal deformability. This particular design is very effective at decoupling the motion artifacts from the desired signals.”
To create this prototype, Nam and colleagues performed several simulations through collaboration with Narayana Aluru, a professor of Mechanical Science and Engineering, and creating novel online software using a nanomanufacturing node. This software system allowed the team to perform simulations before creating a tangible device.
After running the simulation with various designs, the team identified one with superior functions to the others. Graphene emerged as a well-suited material for the job, being that it can withstand significant strain without breaking, unlike many metals and traditional compounds.
Since graphene is a sheet of carbon with a thickness of one atom, the researchers were able to encapsulate the material between two polyimide layers, made of the same material used to protect foldable smartphones. After this durable sheet was prepared, kirigami cuts were made to enhance the material’s ability to stretch.
“Because graphene is sensitive to external changes, yet also a flexible semimetal conductor, people are very interested in creating sensors from it,” Nam said. “This sensitivity is well suited for detecting what is around you, such as glucose or ion levels in sweat.”
This kirigami technique allows for graphene to not only be more stretchable, but strain-insensitive and free from motion artifacts as well. This means that there is no change in its electrical state even when the material is deformed, which is beneficial for wearable sensors that take precise measurements of physiological data. These graphene electrodes achieved a strain-insensitivity up to 240% uniaxial strain, or 720 degrees of twisting.
“What’s interesting about kirigami is that when you stretch it, you create an out of plane tilting,” Nam said. “That is how the structure can take such large deformations.”
This design placed the active sensing element between two bridges of kirigami graphene. The graphene was able to take the load from stretching and straining without losing any electrical signal, allowing the active sensing element to stay connected to the surface. This unique ability of the material to stretch and redistribute stress is attributed to the kirigami technique.
Nam and colleagues are currently working to improve upon this already effective technology and eventually commercialize it. The researchers also had positive results using polydimethylsiloxane (PDMS) as the encapsulating layers and feel that this design could extend to other atomically-thin materials like transition metal dichalcogenides in addition to graphene.
In the next decade, #IoT will have on #clothes with features and performance for #customers and #sports. – Carolina Ramalho ??? https://t.co/QoSFxLPlCc
— Carolina Ramalho (@loracmustaine) October 22, 2019