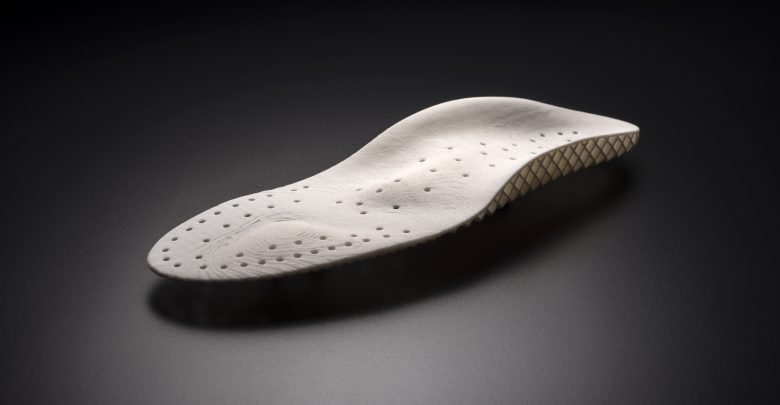
Covestro, a German chemical manufacturer, recently announced that it would be using its Thermoplastic polyurethane (TPU) material to 3D print orthopedic insoles for shoes. A prototype of these fully customizable insoles will be displayed at the K 2019 Trade Fair for Plastics and Rubber in Düsseldorf from October 16-23.
The orthopedic insole is typically customized by hand, requiring a significant amount of time and materials to produce and costing the consumer hundreds in some circumstances. This labor-intensive procedure makes it possible to create these custom orthotics.
3D printing technology not only allows for the insole to be customized perfectly to the unique shape of the patient’s foot, but it cuts out the tedious process of creating these insoles by hand as well. This fast, scalable manufacturing technique is also cheaper than the current approach.
Covestro’s orthopedic insoles are created using an automated and digital process in which a 3D file can be sent to a printer over a far distance. This manufacturing process minimizes waste in creating these custom orthotics as well. The company’s TPU, a thermoplastic material with adjustable flexibility and rigidity, is the material that these insoles are created from. This plastic offers superior versatility in the 3D printing product that is optimal for a medical prosthesis such as the insole.
“Thermoplastic polyurethane is the material of choice for this application thanks to its favorable range of properties,” said Patrick Rosso, Head of Additive Manufacturing at Covestro. “In particular, our TPU products cover a wide range of hardness. The hardness can also be adjusted by changing the printing structure. This allows manufacturers to print shoe insoles that are completely custom-made—with hard or soft contact areas.”
READ MORE: ActivArmor Providing 3D Printed Casts to the Jacksonville Jaguars
Covestro is testing various insole designs to decide which is easiest to make and most durable for the patient. They have formed a partnership with an unnamed company to pursue this development. Not only will these insoles be much easier to produce, but they will offer unprecedented comfort for the wearer.
With many traditional insoles being formed by stiff foam that is not very breathable, current options can be less than enjoyable to wear. The 3D printing procedure can be used to make the insoles porous, bolstering comfort and breathability.
Covestro has worked in the orthopedic realm in the past, with presenting a design for an orthopedic shoe in 2018 at the OT World Orthopedics fair. Their proposed product reduced the production time of these shoes from weeks to a few days.
About Covestro
Founded in September of 2015, Covestro is a Bayer spinoff formerly known as Bayer Material Science. The company produces specialty chemicals for heat-insulating foams as well as plastics, like that used in this insole. Covestro takes pride in creating sustainable solutions to combat climate change, resource depletion, and urban and population growth. The company currently has 16,800 employees who work at roughly 30 sites internationally. Their corporate headquarters is in Leverkusen, Germany.
K2019: Covestro presenting insole 3D printing – European Rubber Journal #3dprinting https://t.co/W2FvqJxSw0
— 3D Printing News (@3DPrintMaven) October 3, 2019