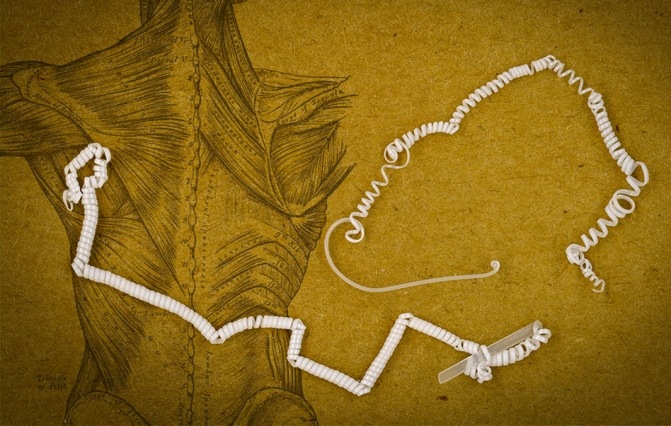
A team of Massachusetts Institute of Technology (MIT) researchers have recently created a system of contractile fibers that could be used like muscles in robotics and prosthetic limbs. Many other approaches have been employed to create artificial muscles, such as motors, hydraulic systems, unique metals, and stimulus-sensitive polymers, however they’ve all fallen short. This new fiber system produced by MIT picks up the slack by imitating a coiling and pulling mechanism, creating lightweight and responsive system. These findings were recently reported in the journal Science.
In an MIT News Office release, the system is compared to the tightly coiled tendrils that sprout from a cucumber plant. These protrusions stretch outward seeking a surface to climb upon, aiming to maximize the sunlight received. The fiber that this team created naturally forms a coil similar to that of the cucumber tendril.
This fiber system was created Methmet Kanik, a postdoc at MIT, and Sirma Örgüç, a graduate student alongside professors Polina Anikeeva, Yoel Fink, Anantha Chandrakasan, and C. Cem Taşan, and five others. The team used a fiber-drawing technique to use two unique polymers in one fiber strand.
These two materials have very different thermal expansion coefficients; therefore, they expand at different rates when heated. This is a similar technique used in thermostats, with two different metals being used to create one metal strip. This strip measures temperature by bending towards the side that expands more slowly at higher temperatures.
The two polymers bonded together are a stretchable, cyclic copolymer elastomer and a stiffer, thermoplastic polyethylene. In combining these two, the researchers created a fiber that tightly coils upon itself after being stretched out multiple times. Interestingly, once Kanik first picked up this coiled fiber, he noticed that it curled up even more tightly.
The team realized that this was simply due to the warmth of his hand. Building on this, they found that the slightest increases in temperature made the coil tighten up. This contraction in response to heat produced a strong pulling force. Once the fiber cooled off again, it expanded to its original form. Anikeeva and colleagues found that the material could undergo this expanding and contracting 10,000 times and still produce strong contractility.
In later testing, the team showed that this process of contracting and expanding could be repeated 10,000 times “and it was still going strong,” Anikeeva says. She claims that this long-lasting contractility in the fiber is due to the moderate conditions it requires, with miniscule changes in temperature producing contractions. The distance of contraction varies from micrometers to millimeters based on heat, and the fiber can easily be made in portions hundreds of meters long.
One single fiber of this dual-material strand can lift loads up to 650 times its own weight. This was discovered using miniaturized testing setups that isolate individual fibers. The amount of tightening that each fiber demonstrates is predetermined in the initial stretching of the fiber. This enables fine tuning of the specific amount of force desired to be generated from a temperature change. In addition, the fibers can be interwoven to produce even stronger contractions.
The researchers also claimed that the manufacturing process allows for any material to be incorporated into the fiber. In this test, they coated the fibers with conductive nanowires to measure the amount of tension exerted by the fibers. For future purposes, they note that internal heating apparatus could be incorporated into the fibers that induces contraction without outside devices.
These fibers hold potential as lightweight, responsive contraction fibers in robotic devices and prosthetic limbs. Prosthetic limbs can be very heavy due to hydraulic or pneumatic actuators, making them uncomfortable for users. By incorporating this lightweight fiber, however, prosthetic limbs may become much more user friendly in the future. These fibers would be optimal for small scale devices like robotic tools that work within an artery, according to Anikeeva.
“We have activation times on the order of tens of milliseconds to seconds,” depending on the dimensions, she says, emphasizing the customizability of these fibers.
My new article is on science magazine cover – Strain-programmable fiber-based artificial muscle https://t.co/KTOPwBVS2C#science, #nature, #MIT, #technology
— Dr. Mehmet Kanık (@mmtkanik) July 11, 2019