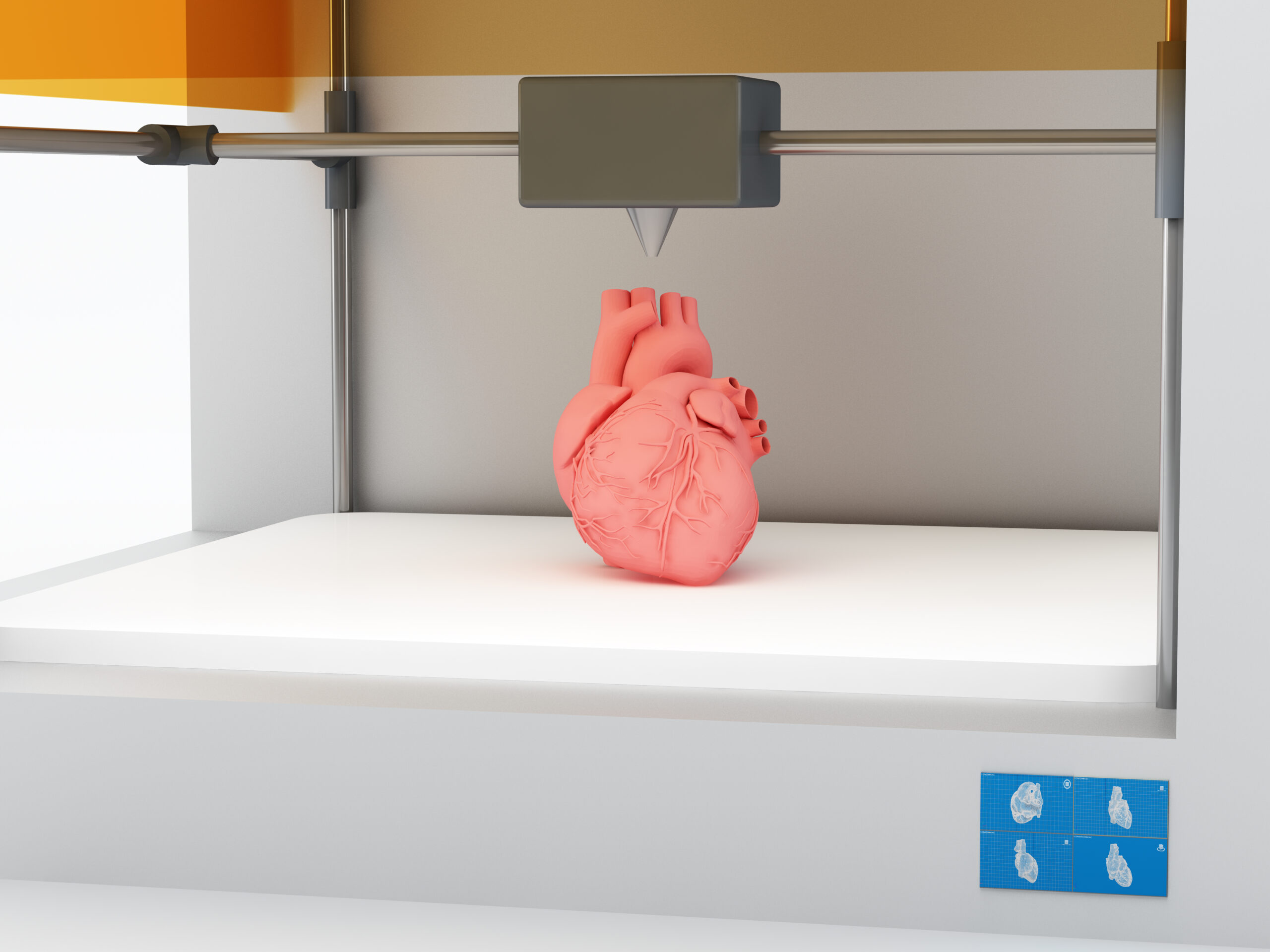
A research team from ETH Zürich, Switzerland and Strait Access Technologies (SAT) has recently been creating 3D printed heart valves using silicone. With an estimated 850,000 people requiring artificial heart valves in 2050, the need for affordable and convenient solutions is imminent. Unfortunately, current heart valve replacements are expensive and labor-intensive to manufacture. By leveraging 3D printing technology, however, these researchers have potentially created a solution to this heart valve dilemma. Their findings were recently reported in the journal Matter.
The valves in the heart function to channel a one-way flow of blood out of a chamber. Faulty valves lead to a backflow of blood into the wrong compartment of the heart, contributing to arrhythmia or heart failure in severe cases. Defects that cause this to happen include valve stenosis (stiffening) and regurgitation (leaking).
When these defects are causing serious risks to one’s health, artificial heart valves can be surgically implanted to intervene. Aging populations, poor diet, and lack of exercise lead experts to predict that the number of valve replacements done will increase dramatically in coming decades. This most recent work with 3D printing is part of a large effort to find scalable solutions to meet this forecasted demand.
Created through additive manufacturing processes, the silicone artificial valve can be customized to each individual patient’s anatomy. This solution allows researchers to model the individual’s valve using CT or MRI images. Unlike with traditional heart valves, this process creates a replacement valve that perfectly fits the patient.
Using radiographic images, the researchers created a digital model to simulate the forces that would act on the silicon implant. This allowed them to evaluate any potential threats to damage and how the implant would hold up. In addition to facilitating blood flow as well as other replacement valve materials, silicon is completely biocompatible as well. Typical replacement valves use hard polymers, metal frames, or animal tissues that pose the threat of rejection. Patients often take life-long immunosuppressants or other drugs to prevent the rejection of these implants. With the silicone implant, this could no longer be an issue.
“The replacement valves currently used are circular, but do not exactly match the shape of the aorta, which is different for each patient,” says co-lead author Manuel Schaffner, touching on the drawbacks of the traditional valve’s rigidity.
This flexible silicone material could potentially create a much stronger seal in the heart chambers. Taking only about 90 minutes to create, this 3D printed solution is much faster than the handmade method that typically takes days.
How the Valve is Made
The implant is created by first making a mold of the valve. Silicone is then sprayed onto this mold to form a thin, flexible replica of the valve’s flaps. The next silicone layer added is much thicker and serves a structural purpose, extending the implant’s longevity. This silicone paste is applied to replicate the collagen fibers that provide dexterity in the human heart valves. The researchers than printed the root of the blood vessel that connects to the heart valve in the same manner, covering it with a stent to connect the replacement valve to the patient’s circulatory system.
The valve’s functionality has been supported through initial testing, and the team hopes to have these valves last for 10-15 years (matching the average time of current replacements).
“It would be marvelous if we could one day produce heart valves that last an entire lifetime and possibly even grow along with the patient, so that they could also be implanted in young people as well,” concluded co-lead author Manuel Schaffner.